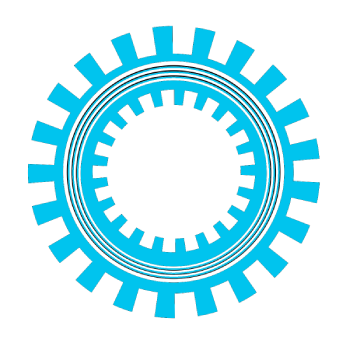
Analyse de revêtements en chrome (XRF)
Cet exemple d’application présente un cas d’analyse des revêtements en chrome en utilisant la méthode de spectrométrie de fluorescence des rayons X dite XRF.
CONTEXTE
Les revêtements en chromage dur sont produits en électrodéposition par une solution contenant de l’acide chromique et de l’anion catalytique en bonne proportion. Le métal produit est très dur et résistant à la corrosion. Le procédé est utilisé pour reconstruire des pièces usagées ou mal usinées pour les tiges de soupape automobile, les segments de piston, les tiges d’amortisseurs, les jambes de force, les alésages diesel et de vérins d’avions, et les axes de transmissions hydrauliques.
Le chromage dur est également appelé chromage industriel, fonctionnel ou technique. Le chrome dur est normalement déposé à une épaisseur allant de 2,5 à 500 μm et pour certaines applications à des épaisseurs considérablement plus importantes. Les principales utilisations du chromage dur sont les applications de résistance à l’usure, l’amélioration des performances des outils, la durée de vie et la récupération des pièces.
L’APPLICATION
Le chromage décoratif est différent du chromage dur par son épaisseur et le type de sous-couche utilisé. le chromage décoratif est très fin, en général l’épaisseur n’excède pas 1.25 μm. Le chromage décoratif est appliqué sur les sous-couches, comme le nickel ou le cuivre/nickel, ce qui confèrent au chrome un aspect cosmétique brillant, semi brillant ou satiné. Le choix des sous-couches, ainsi que le type de chrome appliqué, peuvent également assurer une protection contre la corrosion. Actuellement, la majorité des revêtements décoratifs en chrome sont appliqués à partir de procédés de chrome hexavalent et trivalent.
Pour garantir le bonne fonctionnalité des composants plaqués, les plaqueurs doivent assurer une épaisseur de chrome constante. Le X-STRATA 920 offre une analyse rapide, fiable et non destructive des revêtements en chrome avec un haut de degré de confiance. Le temps de préparation de l’échantillon est très court voir nul. Le système est très simple à utiliser même par les équipes non techniques. La robustesse et la résistance du matériel est adapté aux conditions des environnements de production.
Résultats
Les performances typiques pour des applications courantes et représentatives sont présentées dans les tableaux ci-dessous. La précision a été calculée à partir de la répétabilité de 30 mesures consécutives. La précision est influencée par le temps de mesure, la taille du collimateur, les éléments présents et la gamme d’épaisseur. Dans certains cas, l’erreur peut être réduite en optimisant la plage d’étalonnage pour des applications spécifiques.
Applications STANDARDS
Couche supérieur | 2nde couche | 3ème couche | Substrat |
Cr | – | – | Fe |
Cr | Ni | – | Fe, Stainless Steel, Cu |
Cr | Ni | Cu | Plastics, Zn |
PerformanceS STANDARDS pour une application à une seule couche
Cr/Fe utilisant le collimateur circulaire de 0.3 mm de diamètre.
Substance à analyser | Plage de test | Erreur standard | Précision |
Cr | 0.25-20 μm | 0.025 μm ou 5% d’erreur relative | 1.08 μm pour 20 μm / 0.04 μm pour 1.88 μm |
PerformanceS STANDARDS pour une application avec double coucheS
Cr/Ni/Cu utilisant un collimateur cylindrique de 0.3 mm de diamètre.
Substance à analyser | Plage de test | Erreur standard | Précision |
Cr | 0.46-1.85 μm | 0.025 μm ou 5% d’erreur relative | 0.008 μm pour 0.5 μm / 0.025 μm pour 1.85 μm |
Ni | 4.31-34.5 μm | 10% d’erreur relative | 0.06 μm pour 21 μm / 2.4 μm pour 30 μm |
PerformanceS STANDARDS pour une application avec TRIPLE coucheS
Cr/Ni/Cu/Plastique utilisant un collimateur cylindrique de 0.3 mm de diamètre.
Substance à analyser | Plage de test | Erreur standard | Précision |
Cr | 0.25-1.88 μm | 0.025 μm ou 5% d’erreur relative | 0.02 μm pour 1.88 μm |
Ni | 2.41-10.10 μm | 10% d’erreur relative | 0.08 μm pour 5.08 μm |
Cu | 2.02-14.37 μm | ~15% d’erreur relative | 0.18 μm pour 5.93 μm |
En résumé
La gamme d’analyseurs XRF X-STRATA 920 offre une analyse précise et fiable des revêtements en chrome. Grâce aux normes d’étalonnage traçables de chez Hitachi, les échantillons utilisés en milieu de production peuvent être mesurés simplement et rapidement par des opérateurs de tous niveaux. Les résultats apparaissent en quelques secondes, ce qui permet une optimisation quasi instantanée du processus de production.
Pour en savoir plus sur cet appareil, retrouvez toutes les informations et spécifications de ce produit sur notre page internet dédiée à X-STRATA 920. Vous pourrez également y télécharger une plaquette ou demander un devis.
Découvrir une autre application Demander un devis